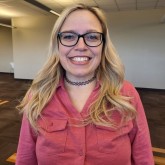
How To Win Over Cautious Consumers This Peak Season
by Lori Boyer
Shoppers are tightening their wallets—and they’re making brands work harder for every sale.
A staggering 54% of U.S. adults plan to spend less this holiday season, and even those who do buy are becoming more deliberate. They’re comparison shopping. They’re hunting for value. And they expect flawless execution once they hit “buy.”
In Peak 2025, trust and value perception are more critical than ever. Small missteps—a vague delivery promise, a clunky returns process, a surprise fee—can drive cautious shoppers away in an instant.
How big brands are adapting
Dollar General is leaning directly into this consumer mindset. The retailer has invested in store remodels and merchandising that emphasize affordable essentials and a fast, efficient shopping experience—perfectly aligned to value-conscious shoppers looking to stretch their dollars.
Many top ecommerce brands are taking a different angle: promise accuracy. Instead of racing to promise the fastest delivery, they’re prioritizing realistic delivery windows—grounded in actual carrier performance. This helps avoid customer disappointment when promised dates aren’t met.
And brands like Nordstrom and Sephora are focusing on post-purchase transparency. Both have invested in branded, real-time tracking experiences that keep customers informed, reduce “Where is my order?” inquiries, and build loyalty through transparency.
How smaller brands can adapt
Smaller brands can absolutely mirror these approaches—often with tools that are already available:
- Leverage real-time tracking to provide transparent, branded updates post-purchase. This builds trust and reduces support tickets.
- Present delivery estimates based on real carrier performance, not generic promises. Accurate dates drive conversion and loyalty.
- Simplify checkout with clear, upfront shipping costs to avoid surprise fees that lead to abandoned carts. (70% of shoppers still abandon carts due to high fees (Baymard).) Offer seamless, self-serve returns—in a cautious buying environment, a great returns experience can be a loyalty driver, not just a cost center.
Why this matters
In a season where shoppers are spending more carefully, clarity, consistency, and trustworthiness win.
Your shipping experience—from checkout through delivery and returns—is a huge part of that equation. Brands that get it right will not only convert more first-time buyers—they’ll earn repeat business in a market where loyalty is harder to build.
Want more strategies? Download our free ebook: Why Peak 2025 Is Different—And How Leading Brands Are Adapting → [Download the ebook]