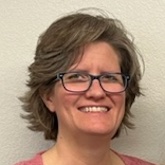
How Smarter Warehouse Load Planning Can Cut Costs and Prevent Shipping Damage
by Marilyn Bunderson
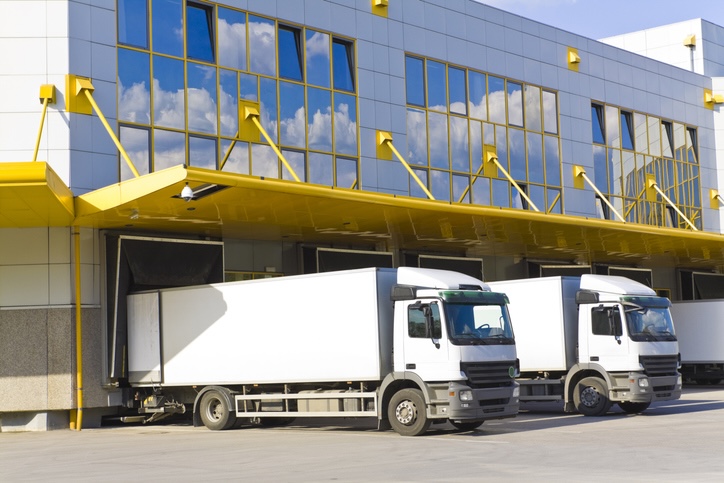
Every action you take—or don’t take—has a consequence. Practically speaking, you need to have a destination in mind with every step you take. That holds true for everything from building a house to loading a pallet or a truck.
Consider this scenario in the style of a popular children’s book:
If you throw a box just anywhere on a pallet, you’ll probably leave a gap.
If you leave a gap, the stack won’t be stable.
If the stack isn’t stable, the pallet might shift during transport.
If the pallet shifts, the boxes could tumble.
If the boxes tumble, products could break.
If products break, you’ll need to file damage claims, and you’ll lose time and money.
If you lose time and money, you’ll need to revisit your packing process.
And if you revisit your packing process, you’ll realize you should’ve taken the time to pack it properly in the first place!
Listen, it’s not all your fault. Most ERPs and WMSs don’t come with cubing software. And if you’re trying to figure out optimal packing and stacking scenarios manually, it’ll slow you down more than you can afford.
Intelligent packing is critical. A well-packed box, a securely stacked pallet, and an efficiently loaded truck are all beautiful in their own way, but even more importantly, they’ll save you money. Lots of it.
The hidden cost of inefficient packing
In the race to fulfill faster and ship smarter, warehouse load planning often gets overlooked. Yet inefficient packing can quietly erode your margins in more ways than one, driving up transportation costs, inflating labor hours, and increasing the risk of product damage in transit.
When boxes aren’t packed with precision, pallets become unstable. When pallets aren’t optimized, you need more of them. And when your truckloads aren’t maximized, you’re shipping air instead of inventory—and who can afford that? Each misstep adds cost and complexity to your supply chain, often without you realizing it.
Smarter warehouse load planning will help you stop the bleeding.
Smarter cartons, pallets, and truckloads
Advanced load planning doesn’t just mean getting more products on a pallet; it’s about making every inch of space work for you. With smarter algorithms and automated tools, modern load planning can do amazing things for your organization:
- Increase packing efficiency: Select the best carton size and packing configuration for each order to reduce dimensional weight and shipping costs.
- Improve pallet optimization: Build stable, space-saving pallet stacks based on product weight, fragility, shape, and orientation rules.
- Maximize truck space: Plan truckloads that fit more product per trip while minimizing the risk of damage due to poor stacking or shifting.
All of this leads to fewer shipments, less damage, less use of materials (think sustainability), and better use of your labor and transportation resources. In other words, lower costs, higher profits, and happier customers.
Make every load count
Warehouse load planning should incorporate cubing software that combines speed, accuracy, and flexibility. With the right solution in place, businesses can integrate directly into a WMS or ERP and also pack and load more efficiently on the warehouse floor.
What businesses can achieve with load planning software:
Packing and palletization automation
Advanced algorithms eliminate human error and guesswork by factoring in product dimensions, weight, and stacking rules. Load planning tools provide clear plans and can even integrate with robotic systems to boost packing speed.
Damage prevention
Properly stacked pallets and efficiently loaded trucks that account for weight and fragility reduce product loss by creating loads that minimize movement and cushion fragile items. Efficient loading tools create load plans for products of any shape and size.
Intelligent scaling
Carton selection and loading plans can be delivered before a warehouse worker has time to think about what box to grab. Cubing software supports growth with high-speed, API-ready tools that work with your existing systems.
Increased efficiency and revenue
Automating complex palletization and speeding carton selection boosts warehouse throughput and reduces labor costs. In addition, optimizing the use of space in cartons increases revenue per carton by 12% to 15%.
How FabFitFun saved millions with load planning
One of the best examples of smart load planning in action comes from FabFitFun, a fast-growing subscription box company known for delighting customers with curated products. As order volumes spiked and warehouse complexity increased in recent years, FabFitFun turned to MagicLogic to streamline operations.
The results were striking:
- 80% of overboxing was eliminated
- 30% to 35% less carton material was used
- Millions saved in shipping each quarter
Read the full FabFitFun case study to see exactly how they did it.
See the full impact of load planning in the ebook
Warehouse inefficiencies don’t fix themselves, and the cost of inaction only rises as order volume grows. Don’t fall into a pattern of inefficiency and end up with damaged goods and wasted space! Smarter load planning with MagicLogic can transform how you pack, palletize, and ship.
Want to see what’s possible when you load smarter?
Download the ebook: The Warehouse of the Future: Smarter, Faster, More Efficient.
This post is part of a 6-part series on the warehouse of the future
Today’s warehouse must evolve or risk falling behind. The writing is on the wall. This series explores key ways warehouses can adapt to keep pace with growing demand and thrive in an ever-changing digital environment.
Read all six posts in the series:
- Why Modern Warehouses Must Evolve To Meet Ecommerce Demand
- How to Automate Warehouse Shipping and Avoid Peak Season Failures
- How Smarter Warehouse Load Planning Can Cut Costs and Prevent Shipping Damage
- When Every Shipment Counts, Visibility Is Everything
- The Warehouse Triple Threat Is Redefining Warehouse Technology
- Is Your Warehouse Future-Proof? Use This 6-Point Checklist