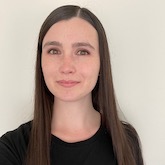
Signs It’s Time To Upgrade Your Fulfillment Tech Stack
by Jaidyn Farar
As December 2023 fades into little more than a memory, it’s easy to forget about the highs and lows of last peak season. But when peak season rolls around again in 2024, you’ll be facing many of the same challenges: an uncertain economy, rising carrier rates, and weather-related supply chain disruptions. To be prepared, it’s important to have the right people, processes, and systems in place—as soon as possible.
The best time to implement new technology is early in the year. If you upgrade your fulfillment tech stack before demand skyrockets, you’ll have plenty of time for implementation, tests, and adjustments. When the holiday season hits, your business will be ready to hit the ground running.
Is your current tech stack capable of handling your current and future shipping volumes? Read on to see if it’s time to change things up.
What does a fulfillment tech stack consist of?
Depending on the stage your business is at, you might rely mostly on manual processes, software, or a mixture of both. If you handle fulfillment in-house, rather than outsourcing to a 3PL, the following systems will become indispensable as you scale:
- Warehouse management system (WMS)
- Inventory management system
- Order management system (OMS)
- Shipping software
- Data and analytics software
Signs your technology needs an upgrade
Implementing new technology can be expensive and time-consuming, requiring hours of work from your internal logistics teams. How can you know when it’s worth making a change? Let’s review five signs it’s high time to upgrade your fulfillment tech stack.
1. Slow response time
During peak season, every second counts. When your goal is to get orders out to customers as quickly and efficiently as possible, you can’t afford to waste time. Did any of your technology become a bottleneck during peak season? If a single system has a slow response time, it can affect every step of the order fulfillment process—even after demand falls to normal levels.
2. Poor efficiency and accuracy metrics
Data doesn’t lie! Data analysis is the most effective way to measure the performance of logistics technology. Analyzing trends and patterns can help you proactively address potential issues.
With reporting and analytics tools, you can generate performance reports to identify efficiency issues in your software. Make sure to get as granular as possible, looking at metrics that relate to specific systems. For example, measuring inventory accuracy will give you insight into how your WMS and inventory management system are performing, and measuring on-time delivery rate will shed light on your shipping software.
3. Excessive downtime
It’s worth repeating: during peak season, every second counts. But peak season isn’t the only time you need to be able to rely on your software. Imagine planning a huge flash sale and having your order management system go out. Or maybe July is one of your busiest months and you experience several outages that delay all your shipments.
To avoid issues during your busiest periods, monitor any downtime or system outages during slower times. If you realize that unplanned downtime is disrupting operations and affecting order processing, communicate with your software provider and consider switching systems if the issues continue.
4. Lack of scalability and flexibility
Some technology works great during a certain growth stage but doesn’t scale with the business. As the volume of orders and the complexity of fulfillment processes increase, these systems struggle to adapt, leading to inefficiencies, delays, and increased operational costs. What’s more, changes in business requirements, market dynamics, or customer expectations can’t be easily accommodated.
Noticing that your technology hasn’t supported business growth? Begin researching solutions that offer scalability and flexibility. To tailor the software to your specific needs, opt for systems that offer customization.
5. Few integration capabilities
Integration allows for real-time data visibility across every stage of the fulfillment process, including inventory management, order processing, and shipment tracking. Access to up-to-date information enables better decision-making and responsiveness to customer questions.
Are your systems currently siloed? If you’re facing challenges due to technology that can’t integrate with other systems, explore other options. Ensure that the software you’re considering can seamlessly integrate with existing business systems, such as ERP, CRM, and ecommerce platforms.
Fulfillment software not making the cut?
So, how does your fulfillment software stack up? As you were reading, you may have realized that one (or more) of your current technologies aren’t working as well as you need them to be. After taking a closer look at their performance—and diving into the data—your suspicions might be confirmed.
If your shipping software has been holding you back, check out EasyPost’s offerings. With a suite of shipping APIs that’s perfect for small- and medium-sized businesses, enterprise shipping software for larger ones, and industry-leading 99.99% uptime for four years in a row, EasyPost will support your shipping operations now and in the future.
We also partner with leading logistics technology companies. If you’re in the market for a new WMS, OMS, inventory management system, or 3PL, we can help you choose the right one.