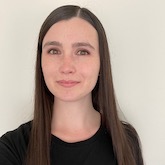
How To Handle Shipping Delays in Your Ecommerce Business
by Jaidyn Farar
Customers hold ecommerce businesses to a high standard, especially when it comes to shipping time. Delays can happen for a variety of reasons, but a consumer only knows one thing: their package didn’t arrive when it was supposed to.
To keep customer satisfaction high, it’s essential to understand what causes delays and take measures to avoid them.
What are shipping delays?
Shipping delays are situations where delivery takes longer than initially expected or planned. Delays can be caused by bad weather, supply chain disruptions, geopolitical events, and more—but regardless of the cause, the effect is usually dissatisfied customers.
The numbers say it all: delays are a common frustration for consumers and businesses alike.
- Eighty percent of people have experienced at least one shipment delay.
- Over half of consumers (53%) say that shipping time is the most frustrating thing about ordering online.
- When asked about the most important attributes of online shopping, 41% of people said fast and reliable delivery.
- When surveyed, 98% of retailers admitted to having pain points when it comes to delivery time.
Why are shipping delays harmful?
In addition to hurting the customer experience, shipping delays cost your business money. Let’s take a closer look at the consequences of delayed shipments.
- Lost business. Over half of consumers continue to shop with brands that deliver goods fastest, and 55% have canceled a delayed shipment due to a bad customer experience. If your packages are delayed—and especially if you don’t respond helpfully—you’re likely to lose customers.
- Damaged reputation. Shipping issues often lead to unhappy customers expressing their frustration through negative reviews, complaints, or refund requests. This harms your reputation and reduces customer trust.
- Increased customer service workload. When shipments are delayed, you’ll see an influx of customer inquiries and complaints. This places a burden on customer service teams, requiring additional time and resources to resolve issues.
Before creating a plan to avoid these negative impacts, you first need to understand the most common causes of delays.
What causes shipping delays?
Shipping delays can be caused by bad weather, geopolitical conflicts, high-demand seasons, and many other factors. In this section, we’ll review a few reasons for delays.
Weather and natural disasters
Storms and natural disasters often disrupt logistics networks. When transportation conditions become unsafe for carriers to operate efficiently, they aren’t always able to deliver packages on time.
According to one report, extreme weather events are the top risk supply chains face in 2024. But weather-related disruptions aren’t always as devastating as a major hurricane or earthquake; something as simple as winter storms can cause major backups.
Global emergencies
Global conflicts disrupt the entire supply chain, causing a ripple effect that leads to delays in procurement, production, and distribution.
In the past several years, several global events have caused severe supply chain disruptions (and delayed shipments). The Covid-19 pandemic, Russia’s invasion of Ukraine, and—most recently—the Red Sea crisis are just a few examples.
Labor issues
When carriers and other logistics providers face strikes and labor shortages, their delivery accuracy and efficiency go down. Without enough warehouse workers and drivers, they simply can’t handle high shipment volumes.
For example, take the potential UPS strike of 2023. If the 340,000 workers had walked out, it would have wreaked havoc on many businesses’ order fulfillment operations. Although the strike was averted, it emphasized the importance of not relying on a single carrier to deliver packages.
Holidays and high-demand seasons
During national and international holidays (especially the peak season between October and January), increased shipping volumes and reduced working hours can overwhelm carriers and logistics providers, causing delays in parcel processing and delivery.
Your business’s internal fulfillment processes also affect shipping speeds during peak season. If your pick-and-pack processes aren't set up to scale to demand, bottlenecks in the warehouse will result in late deliveries.
Customs
Shipping internationally? Customs processing can introduce delays as packages undergo inspections, documentation checks, and clearance procedures.
Incorrect shipping data
Inaccurate or incomplete shipping information can lead to misrouting or the need for additional verification. Including the correct recipient addresses on shipping labels is especially essential for avoiding these kinds of delays. By using address verification software, you’ll catch mistakes and typos before they cause major issues.
Technology
Automating your shipping processes helps you get more done with less labor and money. But what happens when your software or equipment fails? Technical issues, glitches, and downtime interrupt automated tracking, sorting, and delivery processes. In short, if your software provider isn’t reliable, you could find yourself facing major shipping delays.
Reliability is especially essential when it comes to shipping software. When you’re shipping thousands of orders a day, even a few minutes of downtime causes major delays as packages pile up in your warehouses but can’t be labeled or shipped. To avoid outages, look for shipping software with industry-leading reliability.
How to handle shipping delays like a pro
With the right people, processes, and technology, you’ll be prepared to handle shipping delays like a pro. In this section, we’ll break things down into two phases: preparing for delays and responding to them.
Preparing for delays
Delays are inevitable. Unless you can control all the factors listed above—weather, geopolitical issues, etc.—you’ll eventually encounter them. However, you can take steps ahead of time to lessen their negative impacts.
Plan for worst-case scenarios
Because you know what causes shipping delays, you have the power to plan ahead to avoid or mitigate the impact of disruptions. As you review possible disruptions to your shipping, develop contingency plans for each one.
For example, if a bad storm strikes one of your distribution centers, will you fulfill orders out of a different facility? If a major carrier faces a labor strike, which backup carriers will take on your volume?
By doing the hard work of planning and preparation now, you’ll make things easier on yourself when disaster strikes.
Track packages
Tracking packages is one of the best ways to prepare for shipping delays. By collecting and analyzing tracking data (using software like EasyPost Analytics), you gain insight into what’s causing delays. Once you identify patterns, you can take action to smooth out processes for the future.
Tracking also helps you meet customer expectations—68% of people expect to know where their order is throughout the delivery process at all times.
Monitor your supply chain
In addition to tracking packages, remember to keep an eye on every element of your supply chain. After all, if you don’t have products in stock when customers order them, you won’t be able to ship them on time. Maintain open communication with suppliers, staying informed about their policies, potential challenges, and any changes in their operations.
Allow extra shipping time in case of delays
Many customers want 2-day shipping, but with such a short delivery window, the potential for things to go wrong increases. Consider offering longer delivery times to account for unforeseen delays. To help this go over well, make shipping “free” by calculating shipping costs ahead of time and incorporating them into product prices.
Data suggests that this strategy can be an effective way to ease customer concerns about delivery times. In one survey, just 32% of consumers ranked delivery speed among the most important factors when choosing an online retailer, while 59% valued free shipping. Many people accept longer shipping times—and are more forgiving of delays—when they’ve saved money on their purchase.
Use multi-carrier shipping software
Multi-carrier shipping software helps you plan for the worst-case scenario. Rather than manually integrating with backup carriers, you’ll automatically have access to a wide range of national, regional, and local carriers. If one partner runs into trouble, you can temporarily funnel your shipping volume to others.
With the past few years bringing one shipping disruption after another, many businesses have realized the necessity of a multi-carrier strategy. Between September 2019 and September 2022, the number of carriers the average shipper worked with increased by 42.5%.
Responding to delays
When delays happen despite your best efforts, customer service is key; 91% of consumers say that a good customer experience makes waiting for a product bearable.
Notify recipients
Packages running behind? Communicate delays to customers through your website, emails, and order confirmations. After notifying them, provide clear and transparent information on the reasons for the delay, as well as revised delivery estimates.
Acknowledge the impact on the customer and assure them you’re actively working to address the situation.
Use hold at location options
Many carriers offer hold at location services that let you redirect a package after it’s been shipped. The package will be sent to a certain location (often a carrier’s store), where the recipient can pick it up in person. This can help minimize some of the delays that last-mile delivery entails.
If last-mile delivery in their area is particularly slow (due to long distances or traffic congestion), customers may also appreciate the option to choose in-person pickup during checkout. If possible, allow people to order online and pick up their products at one of your store locations.
Compensate customers for late deliveries
Late packages put a damper on people’s days—and their plans. As a gesture of goodwill, establish a fair and transparent refund policy for situations where delays significantly impact the delivery experience. Clearly communicate this policy to customers and apply it consistently.
If a full refund isn’t doable, consider providing some other form of compensation (like a gift card or generous discount) to minimize customer dissatisfaction.
Improve for the future
If delays continue to happen due to issues with suppliers or carriers, reassess these partnerships. Consider alternatives with more reliable services to minimize the risk of future delays.
If delays stem from issues within your distribution centers, you’ll need to evaluate and optimize your pick and pack processes. Not sure where to get started? Bring in outside experts who offer guidance on warehouse setup, WMS implementation, and more.
Keep shipments on time with EasyPost Enterprise
Shipping delays don’t need to stand in the way of a great delivery experience. By following the best practices above, you’ll be prepared to handle them—and EasyPost Enterprise can help.
Designed for high-volume shippers, EasyPost Enterprise can keep up during even the busiest times of the year. It comes with sub-second shipping, data analytics visibility, real-time tracking, world-class support, and more. And with 99.99% uptime, EasyPost Enterprise will keep your shipments on schedule—no matter what.
Get in touch with our team to learn how EasyPost Enterprise fits into your logistics strategy.