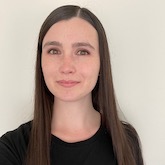
What Is Logistics Management?
by Jaidyn Farar
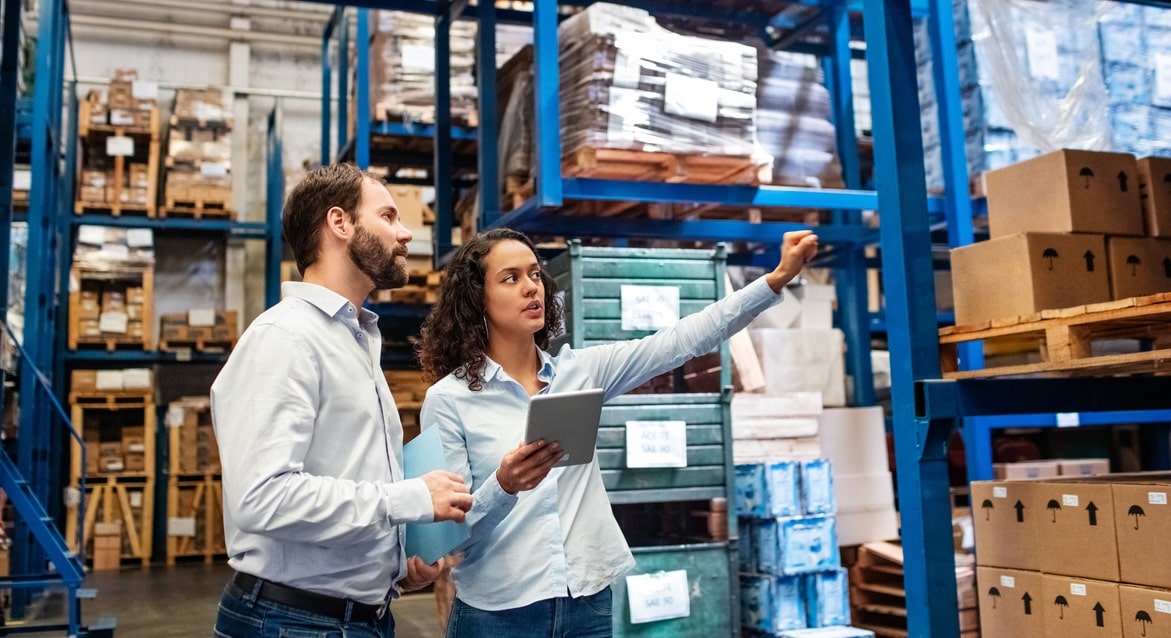
Effective logistics management is critical to a business’s success. What does it involve, and how can you optimize your processes? Read on to find out!
What is logistics management?
Logistics management is the process of coordinating how goods move from one place to another—whether that’s from suppliers to warehouses, warehouses to customers, or anywhere in between.
It involves managing procurement, inventory, warehousing, transportation, order fulfillment, and more.
Because logistics management deals with supply chain efficiency, it directly impacts costs and customer satisfaction. With well-run logistics, businesses ensure products arrive on time, minimize waste, and keep shipping costs under control—all of which can make or break their success.
Who is a logistics manager?
A logistics manager is the person responsible for overseeing the transportation, storage, and distribution of goods. A skilled logistics manager is adept at problem-solving, negotiation, data analysis, and communication.
Types of logistics management
The three types of logistics management are inbound, outbound, and reverse. Let’s look at what each one entails.
Inbound logistics management
Inbound logistics focuses on moving raw materials, supplies, and goods into your business. For example, purchasing inventory from a supplier and planning to receive it at your warehouse is considered inbound logistics management.
Efficient inbound logistics helps businesses avoid delays, reduce costs, and maintain steady operations.
Key tasks include:
- Coordinating shipments from suppliers
- Managing inventory levels and warehouse stocking
- Negotiating shipping rates and terms
- Tracking shipments and resolving delays
Outbound logistics management
Outbound logistics involves delivering finished goods from fulfillment or distribution centers to customers or retailers. Strong outbound logistics keeps customers happy and reduces shipping-related costs.
Key tasks include:
- Processing and fulfilling customer orders
- Managing picking, packing, and shipping
- Coordinating with carriers and delivery partners
- Tracking shipments and handling delivery issues
Reverse logistics management
Reverse logistics deals with the movement of goods back through the supply chain from a customer to a business. It’s typically due to returns, but customers may also send items back for repairs or recycling.
Good reverse logistics management will ensure that returns are handled efficiently, minimizing waste and maximizing the value recovered from damaged, defective, or unwanted products.
Key tasks include:
- Managing customer returns and exchanges
- Coordinating repairs, refurbishment, recycling, or disposal
- Reducing waste through resale strategies
- Streamlining return shipping processes to cut costs
Logistics management functions
Logistics management encompasses a wide variety of activities. This section will touch on some of the most important ones, beginning with sourcing and procurement.
Sourcing and procurement
Sourcing and procurement are all about making sure your business gets the right materials or products at the right price, without sacrificing quality or reliability.
While cost plays an important role in procurement, building strong relationships with suppliers is just as important. By negotiating strategically, being upfront about your needs and requirements, and communicating when issues arise, you’ll stay on good terms with suppliers and get great service.
Production planning and scheduling
If your business involves manufacturing, production planning keeps things running smoothly. This process determines what needs to be made, when, and in what quantity to meet customer demand.
A well-structured plan balances efficiency with flexibility—because no matter how well you plan, unexpected issues will pop up.
The best logistics managers use forecasting tools, real-time production tracking, and just-in-time inventory strategies to avoid slowdowns and keep production aligned with demand.
Warehousing
Warehousing includes all the activities necessary to store and organize inventory so that everything is accessible, secure, and ready to move when needed.
A poorly managed warehouse often leads to logistical disasters. (Think: misplaced inventory, delayed shipments, and higher costs across the board.)
On the other hand, a well-managed warehouse provides lots of opportunities to save money and boost customer satisfaction. Smart businesses optimize their warehouse layouts, invest in tracking technology like RFID or barcode scanning, and use automation—including robotics—where it makes sense.
Materials handling
Every time a product moves within your facility—whether it's being unloaded, stored, or packed—there’s an opportunity for inefficiency, damage, or even workplace injuries. Materials handling focuses on reducing those risks, making internal movement as fast and safe as possible.
Inventory management
Inventory management deals with finding the perfect balance between having too much inventory (which ties up cash and storage space) and having too little (which can lead to stockouts and lost sales).
This means tracking stock levels in real time, predicting demand accurately, and setting up smart reorder points to avoid last-minute rush orders. Businesses that get inventory management right use tools like demand forecasting, automated replenishment, and regular cycle counts to keep everything running smoothly.
Order processing and fulfillment
Order processing and fulfillment are all about getting products picked, packed, and shipped accurately and on time. This includes a variety of activities:
- Receiving orders
- Checking available stock
- Processing payments
- Picking
- Packing
- Shipping
- Updating inventory
- Processing returns
Fulfillment is one of the most important aspects of logistics. Mistakes here can lead to unhappy customers, costly returns, and even damage to your reputation. On the flip side, fulfilling orders quickly and accurately leads to happier, more loyal customers.
Packaging
Packaging affects everything from shipping costs to product protection. Use the wrong materials, and you risk products getting damaged in transit. Use excessive packaging, and you’re driving up costs.
The best approach? Strike a balance by choosing packaging that’s durable, cost-effective, and optimized for shipping efficiency.
Transportation management (shipping)
Once your products are packed and ready to go, transportation management ensures they reach the correct destination on time. Whether you’re handling parcel deliveries or freight shipments, you have a lot to juggle: carrier selection and performance monitoring, real-time tracking, and more.
Shipping products to customers is one of the most expensive logistics processes, and most companies are always looking for ways to keep costs down.
But to manage transportation well, you shouldn’t just look for the cheapest option. In addition to cost, you’ll want to consider reliability and speed. To find the best balance, consider using shipping software like EasyPost Enterprise to integrate with multiple carriers and compare rates and services.
“[Determine] what cost targets you have … and also the service and transit time, delivery reliability, delivery speed. … And then look at [your shipping] and see where the gaps are. If you aren't meeting objectives, then the current providers [are] contributing to that in some way. That's where you can look for opportunities to find the right partners to help close those gaps.” — Nate Skiver, Costs, Carriers, and China: Parcel Shipping in 2025
Third-party logistics provider (3PL) management
Some companies outsource part or all of their order fulfillment to a third-party logistics provider, or 3PL. When this is the case, logistics management involves coordinating and overseeing that relationship.
Outsourcing logistics isn’t as simple as signing a contract and hoping for the best; you need clear service agreements, regular performance tracking, and open communication to make sure your fulfillment partner is delivering what you need.
Logistics management best practices
The way you handle logistics management has a huge impact on your efficiency and customer satisfaction. Implementing a few simple best practices will help your business thrive—even as rising logistics costs and other challenges come your way.
Automate processes
More and more organizations are turning to technology to offset the effects of rising shipping rates and labor costs. In fact, one survey found that 87% of shippers have maintained or grown their technology investments since 2020, while 93% plan to maintain or increase spending in the coming years. It’s clear that logistics systems are the way forward for businesses that want to stay competitive.
Automation speeds up processes, decreases costly errors, and saves on labor costs. The benefits are undeniable—but where should your business begin?
A great starting point is warehouse management systems (WMS) that automate inventory tracking, order picking, and restocking. Automated picking systems, such as robots or conveyor belts, can drastically speed up fulfillment while reducing labor costs.
When it’s time to deliver customer orders, shipping platforms simplify carrier integration, shipping method selection, label generation, and tracking.
Remember, you don’t have to dive in feet-first with automation. Even small changes can lead to big savings and efficiency gains. No matter what you can afford to invest initially, the key to getting started is to identify repetitive tasks that don’t require human decision-making and let technology handle them.
Base decisions on real-time data
Good logistics management rests on a foundation of informed decisions based on up-to-the-minute data. Without real-time data, you’ll likely react to problems too late, leading to extra costs and fulfillment slowdowns.
To avoid this, invest in real-time tracking systems that monitor shipments, inventory levels, and warehouse operations. With full visibility into your supply chain, you’ll be able to respond immediately to shipping delays and prevent stockouts before they become a problem.
Make contingency plans
Even the best logistics strategy will run into unexpected disruptions: an inbound inventory shipment gets delayed, a carrier shows up late for a package pickup, or a global conflict shuts down ports.
Whatever the case, you need to have a backup plan in place. Businesses that plan for disruptions recover faster and minimize losses.
The following ideas will help you start preparing for logistics nightmares so they don’t catch you off guard:
- Have backup suppliers. Have backup suppliers lined up in case the primary source fails. It’s helpful to use suppliers located in different parts of the world. That way, if a new tariff is enacted or a conflict arises in a specific country, you can rely on the suppliers that aren’t affected.
- Diversify your shipping. With a multi-carrier shipping strategy, if one carrier is backed up or faces a labor strike, there’s an alternative ready.
- Don’t forget about warehouses. Create emergency response plans for warehouse disruptions, detailing what to do if operations suddenly shut down.
The importance of logistics management
Logistics management is crucial for keeping goods and materials moving efficiently through the supply chain. In addition to saving money, it directly impacts customer satisfaction. After all, what consumer doesn’t enjoy getting products delivered on time, in perfect condition, and at a reasonable cost?
Specific benefits of logistics management include the following:
- Reduces costs
- Improves delivery speed and reliability
- Minimizes product damage
- Boosts customer satisfaction and retention
- Strengthens supplier and carrier relationships
Level up your logistics management with EasyPost Enterprise
Now that we’ve answered the question “What is logistics management?” you probably have an even more pressing question on your mind: “How can I handle logistics management more efficiently?”
It all starts with having the right systems in place. Designed for high-growth shippers, EasyPost Enterprise logistics management systems help businesses simplify logistics management, save money, and improve customer satisfaction with:
- On-premise/cloud-enabled shipping software
- Label and form generation
- Data and analytics dashboard
- Consulting services
- Load planning
Find out which EasyPost Enterprise solution is right for you.